Am Ende läuft ein Gerät in der Größe einer Mikrowelle vom Fließband: An dieser Vision arbeitet das ELEFACT-Projektteam mit der automatisierten Fertigung von modularen, flexiblen Elektrolyseuren. Das senkt nicht nur die Kosten für grünen Wasserstoff, sondern ermöglicht auch einen deutlich effizienteren Betrieb.
Jan Tiemeyer und Jerrit Hilgedieck sind bereits vor mehr als einem halben Jahr an ihrem neuen Arbeitsplatz in Saerbeck eingezogen. Die beiden Ingenieure arbeiten am dortigen Campus der Enapter GmbH im Rahmen des Projekts ELEFACT an der Massenfertigung von innovativen Elektrolyseuren mittels Anionenaustauschmembran (AEM-Elektrolyse). Ziel ist es, die bisher in Handarbeit realisierte Fertigung in einen industriellen Maßstab zu überführen.
Das Projekt auf einen Blick
Kurztitel: ELEFACT
Projektname: Innovative Entwicklung von Maschinen-Blueprints für die AEM Massenfertigung
Projektpartner: Enapter GmbH (Berlin) und Fachhochschule Münster
Projektstart: 15.06.2021
Projektlaufzeit: 4 Jahre
Förderrichtlinie: progres.NRW – Innovation
Fördersumme: 11.228.362,93 Euro
Die AEM-Elektrolyse ist noch ein relativ junges Verfahren, das in den letzten Jahren entwickelt wurde. Die Qualität dieser neuen Technologie liegt in einer Kombination der jeweiligen Vorteile der bisher vorherrschenden Elektrolyseverfahren. Sie vereint sowohl die Stärke der Alkalielektrolyse – nämlich die Verwendung kostengünstiger Materialien – als auch die hohe Flexibilität des Proton-Exchange-Membrane-Verfahrens (PEM-Elektrolyse) in sich.
Mit automatisierter Massenfertigung Kosten für grünen Wasserstoff reduzieren
Der Vorgänger dieser innovativen Geräte wird in Pisa bereits seit 2019 von einem Schwesterunternehmen der Enapter GmbH in Serie gefertigt. Im Projekt ELEFACT entwickelt, erprobt und implementiert das Projektteam der Enapter GmbH und der Fachhochschule Münster (FH Münster) jetzt die notwendigen Automatisierungselemente für eine Massenfertigung von AEM Stacks und -Elektrolyseuren.
Seinen Namen hat der Saerbecker Elektrolyseur in Anlehnung an ein Automobil von Ford erhalten, das weltweit als erstes in Fließbandfertigung hergestellt wurde.
Das Modell T von Ford war das erste Auto, das einer breiteren Masse zugänglich war, weil mit der großtechnischen Fertigung vom Band die Kosten erheblich gesenkt werden konnten. Dasselbe Ergebnis erwarten wir bei unserem Modell-T-Elektrolyseur, wenn wir automatisiert in größeren Mengen produzieren und entsprechende Skaleneffekte erreichen.
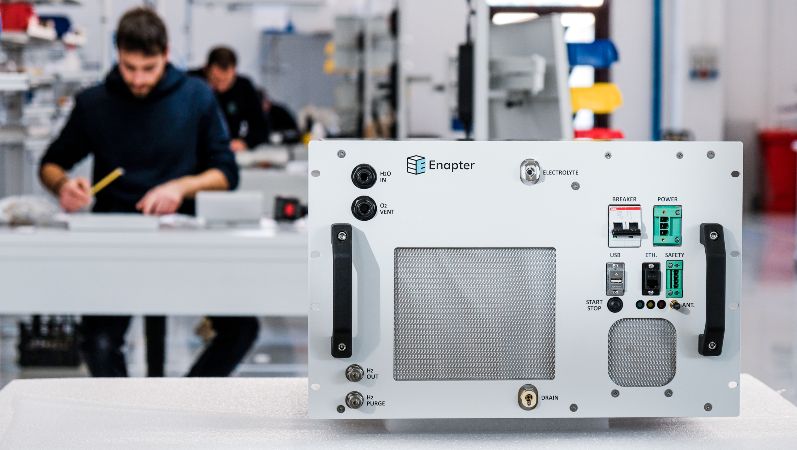
Vom Labor-Teststand zur industriellen Fertigungshalle
Das Projekt ELEFACT ist in fünf Arbeitspakete unterteilt, die den gesamten Herstellungsprozess – also von der Fertigung der Chemierohteile bis hin zur automatisierten Produktion – abdecken. Die ersten beiden Arbeitspakete bilden vor allem den chemischen Bereich ab. Dabei geht es um die Fertigung der chemischen Substanzen, die für den sogenannten Stack benötigt werden. Der Stack ist das Herz des Elektrolyseurs, dort wird der Wasserstoff am Ende produziert. Aktuell überprüfen die Forschenden das Herstellungsverfahren der Chemiebestandteile in einem Teststand an der FH Münster. Diese Produktionsanlage spiegelt sozusagen die erste Ausbaustufe der späteren Massenfertigung wider und ermöglicht eine detaillierte Untersuchung verschiedener Prozessparameter und Materialien im laufenden Betrieb. In einem nächsten Schritt fließen die so gewonnenen Erkenntnisse in die Konzeptionierung für eine industrielle Fertigung im größeren Maßstab ein.
Die Endproduktion der Elektrolyseure wird in einer großen Fertigungshalle am Campus in Saerbeck umgesetzt. Basierend auf den bisherigen Ergebnissen seit Projektstart im Juni 2021 haben die Forschenden mehrere Konzeptstudien durchgeführt, wie die Anlagen und Maschinen passgenau aufeinander abgestimmt und aufgebaut werden können.
Von Maschinenplanungsseite haben wir uns bereits intensiv mit Lieferanten ausgetauscht und Spezifikationen entwickelt, wie so eine Produktionsanlage bzw. Teilanlage genau aussehen muss. Wir überprüfen zudem kontinuierlich, ob unsere Überlegungen im laufenden Betrieb standhalten und nutzen die Ergebnisse zur weiteren Optimierung unserer Anlagenplanung.

Planung und Beschaffung für die automatisierte Fertigung
In allen Arbeitsbereichen stehen die Forschenden bereits im Austausch mit Firmen, haben Konzepte erstellt oder auch erste Angebote für Produktionsanlagen vorliegen. Zeitgleich werden sowohl das Produkt selbst als auch das Herstellungsverfahren stetig überprüft und bei Bedarf entsprechende Optimierungsrunden gefahren. Denn im Rahmen der industriellen Fertigung ist es wesentlich schwieriger, die Handhabung einzelner Komponenten später noch einmal anzupassen oder zu verändern, als dies beispielsweise bei der händischen Montage der Fall ist. Ziel ist es daher, das Gerät bis ins kleinste Detail so zu überarbeiten, dass eine industriell fertigbare Version entsteht. Erst mit diesem Wissen gehen die Forschenden an die Beschaffung der Fertigungsmaschinen, um deren Funktionalität und damit die wirtschaftliche Rentabilität sicherzustellen.
Den ursprünglich angedachten Zeitplan musste das Projektteam jedoch anpassen. Das liegt vor allem in einem Anstieg der Kosten und der Lieferzeiten für eine Vielzahl der einzelnen Anlagenbestandteile. Beispielsweise sind die Kosten für eine Maschine, die zu Projektbeginn mit einem Anschaffungswert von rund 1 Million Euro beziffert wurde, zwischenzeitlich auf das sieben- bis achtfache angestiegen. Auch ein enormer Anstieg bei den Lieferzeiten hat zu entsprechenden Verzögerung im Projektplan geführt. Dass die industrielle Fertigung in Saerbeck umgesetzt wird, steht jedoch außer Frage – auch wenn der genaue Zeithorizont noch nicht vollständig absehbar ist.
Modell-T-Elektrolyseur: flexibel und kostengünstig
Die Forschenden sind überzeugt, in jedem Fall die Massenfertigung ihres Kern-Know-hows – nämlich die Chemie- und die Stack-Produktion – bis Projektende in Saerbeck realisieren zu können. Beide Bestandteile werden im Modell-T-Elektrolyseur verbaut, der dadurch in hohen Stückzahlen angefertigt werden kann – was eine erhebliche Reduzierung der Kosten bedingt. Die Modell-T-Elektrolyseure haben gegenüber den Konkurrenzprodukten noch einen weiteren Vorteil: Sie sind relativ klein und zudem modular aufgebaut, was einen flexiblen Einsatz ermöglicht. Sie haben in etwa die Größe einer Mikrowelle und können, je nach konkretem Bedarf, in variierender Stückzahl zum Einsatz kommen. Das ermöglicht einen präzisen und damit deutlich effizienteren Betrieb.
Der Ansatz hinter unserem Modell T lässt sich gut mit Solarpanelen vergleichen, die viele Menschen bereits auf dem Dach haben. Die Module sind immer komplett gleich aufgebaut – und wenn ich mehr Sonnenenergie produzieren möchte, schraube ich ein zweites oder drittes Modul auf´s Dach. Analog dazu stelle ich mir einfach einen zweiten oder dritten Elektrolyseur in die Garage, wenn ich mehr Wasserstoff brauche
Containerlösung für großindustrielle Anwendung
Allerdings stößt dieses Konzept irgendwann an seine Grenzen, möchte man in wirklich große, industrielle Bereiche gehen. „Man kann sich ja nicht unendlich viele von diesen kleinen Geräten in der Größe einer Mikrowelle in die Halle stellen“, erklärt Jerrit Hilgedieck. Diese Herausforderung hat die Forschenden auf eine neue Idee gebracht. In einem parallelen Forschungsprojekt (HY-Core) entwickeln sie eine Containerlösung, in der das Herz der Modell-T-Elektrolyseure hundertfach zum Einsatz kommt. Konkret wird der im Rahmen von ELEFACT entwickelte Stack in eine Art Schuhkarton eingebaut, was die restliche Peripherie der „Mikrowelle“ in hoher Zahl überflüssig macht – diese wird dann nur einmal in größerem Maßstab benötigt. Je nach konkretem Bedarf können dann bis zu 420 dieser Schuhkartons in einem Container verbaut werden – was wiederum einen flexiblen und damit wirtschaftlichen Betrieb ermöglicht.
Im HY-Core-Projekt entwickeln wir unsere großindustrielle Containerlösung als völlig neues Produkt. In ELEFACT konnten wir den Fokus der Produktion der Elektrolyseure zwischenzeitlich erweitern. Denn die zuvor entwickelten Stacks können wir gleichermaßen in den kleineren Geräten als auch in der Containerlösung einsetzen, was den Nutzen der Produktionsmaschinen ungleich erhöht – und zeitgleich die Kosten für den Wasserstoff noch einmal massiv absenkt.
Stand: September 2023
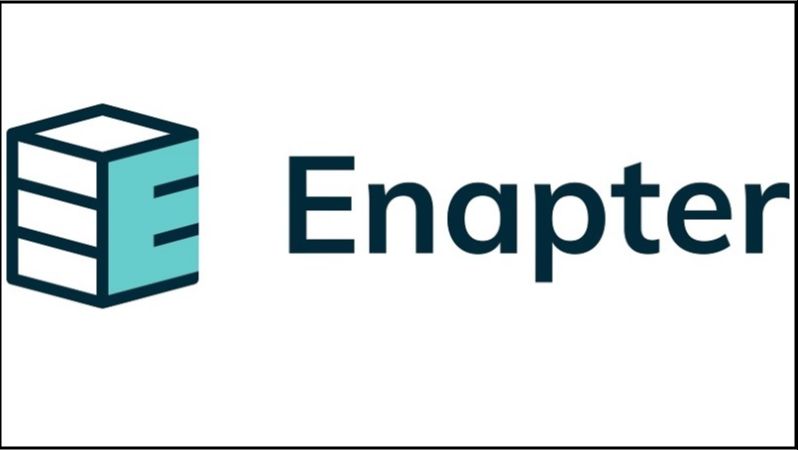